Got a Jackson Performer PS2 currently under construction. Filled the 2 single coil cavities and put a real carbon fiber top on it, currently working on the headstock carbon fiber and trying to find somewhere I can get a brushed silver jackson decal for it....
Workin' on the body:
Template for the Carbon Fiber:
Sanding the Edges:
Routed cavities.....
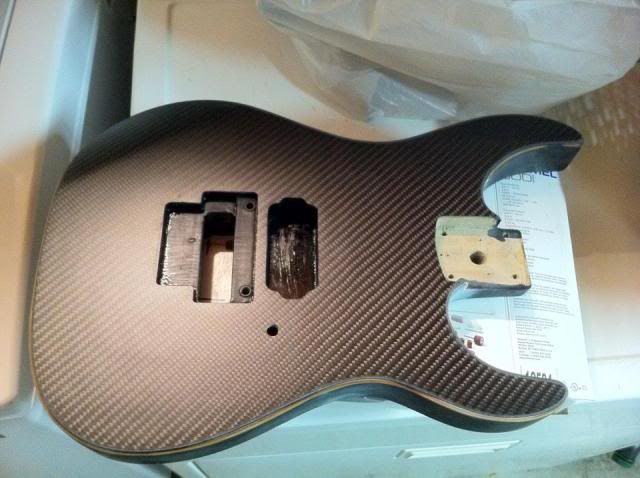
More to come!!!
Workin' on the body:
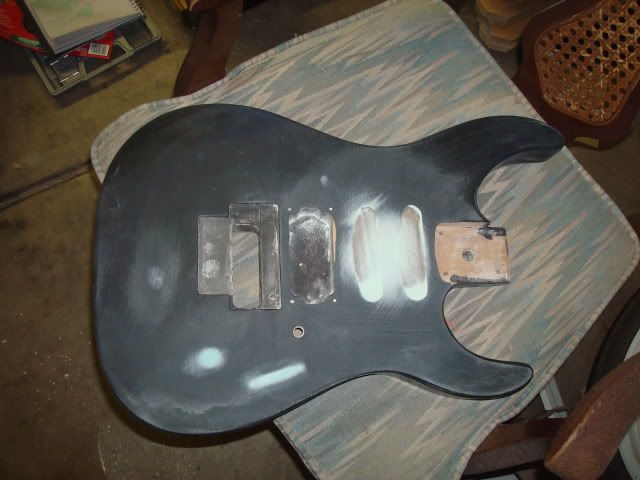
Template for the Carbon Fiber:
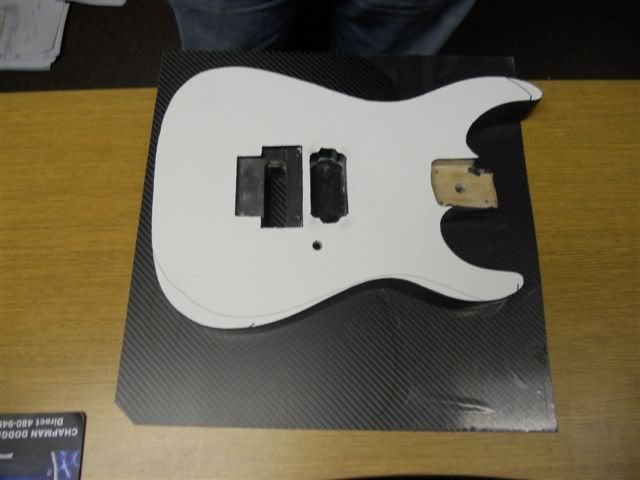
Sanding the Edges:
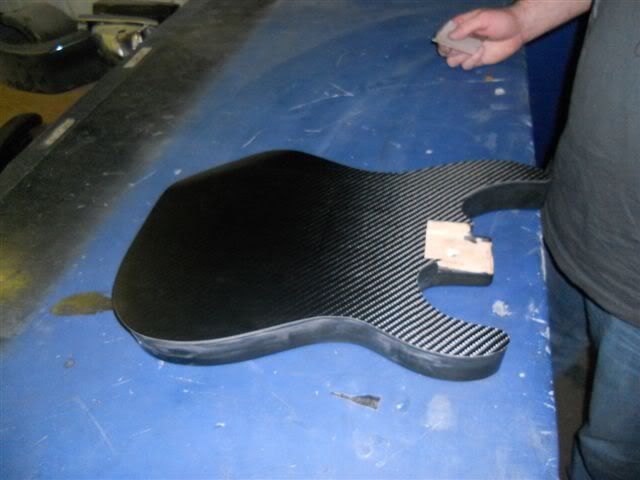
Routed cavities.....
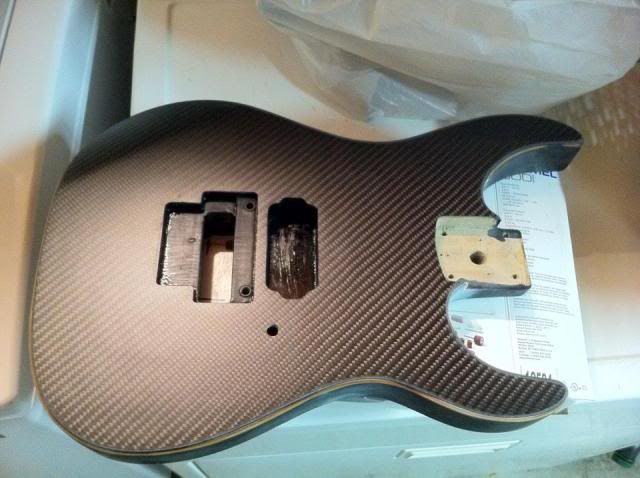
More to come!!!
Comment